So here we are…ready for the “big show”…but not quite at the big show. Think of it this way…to get to zero energy conservation takes us most of the way…and the last bit is the renewables piece. We were here before…. BSI-081: Zeroing In, October 2014. Back then we kinda figured that 70 percent of the way to get to “net zero” was conservation…. Turns out that was a pretty good estimate. Over time lots of folks agreed. Guess what…we changed the building code to get us there. Huh? Yup, if you build new homes to comply with the 2021 International Energy Conservation Code (IECC) you “officially '' comply with the Department of Energy “Zero Energy Ready Home Program (ZERH)”. Okay, there are few other typical “government” things (see https://www.energy.gov/eere/buildings/zero-energy-ready-home-program) but I never thought we would get as far as we did. Nice job United States of America….
Build to the “code” …. Build to the 2021 IECC… and you also qualify for the 45L Tax Credit….(see https://www.energy.gov/eere/buildings/section-45l-tax-credits-zero-energy-ready-homes).
Do this and add about 5kW to 7.5kW of PV to the typical house and you are at “net zero energy”.
So what does this really “mean”? What do you really need to do “construction wise”? Read on. I have taken the IECC climate zones (Figure 1) and provided building sections for each climate zone meeting the 2021 IECC code. There are countless permutations and options….I arbitrarily picked a few “typical” approaches. There is a much longer list of building sections that meet the requirements at the following link: (https://basc.pnnl.gov/building-assemblies) Thank Pacific Northwest National Laboratory for all their efforts.
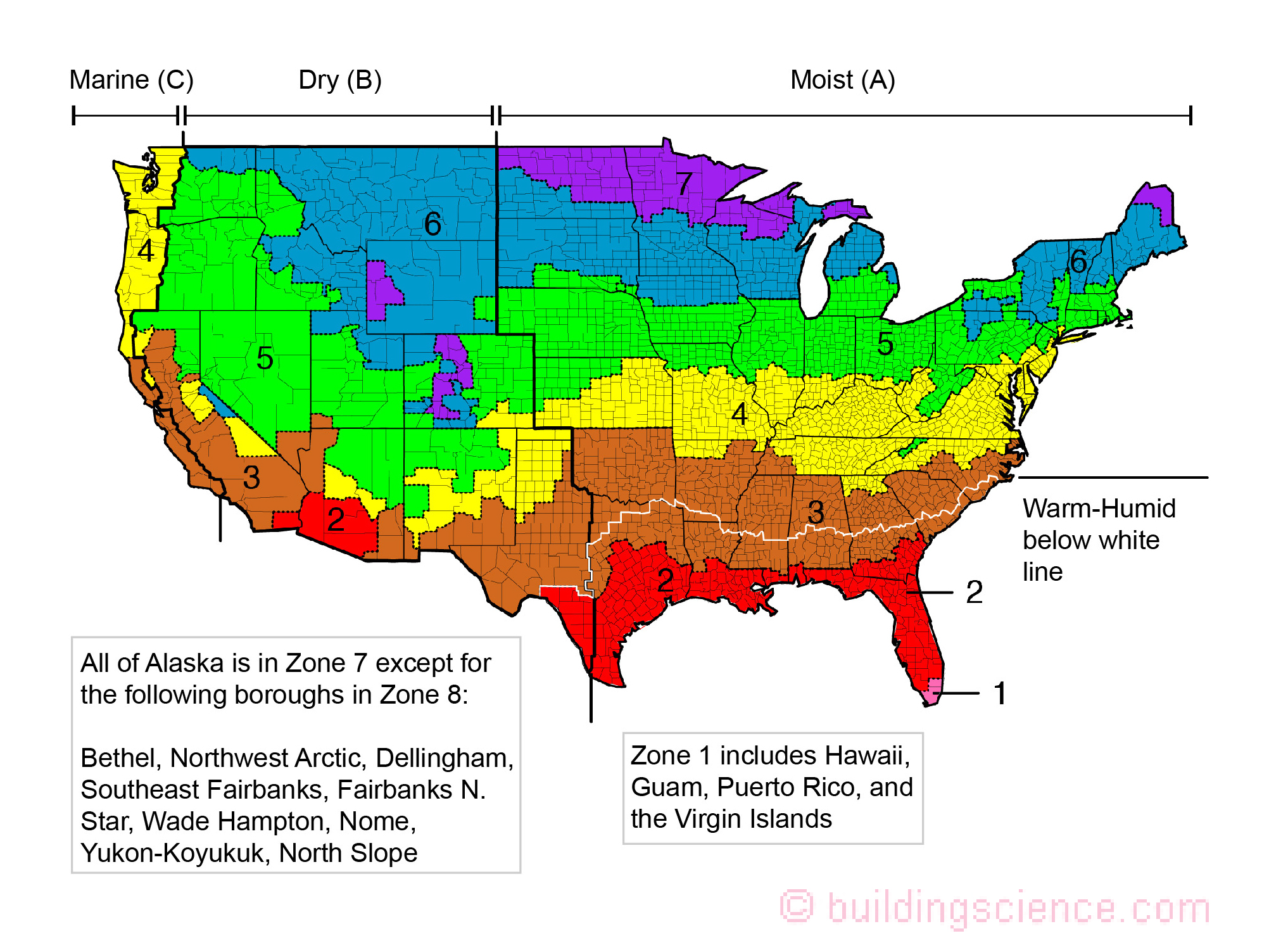
Figure 1: International Energy Conservation Code (IECC) climate zones.
IECC Climate Zone 2A: Unvented Attic with Spray Foam at Roof Deck, 2x6 Wall/CMU Wall, Elevated Slab (Figure 2)
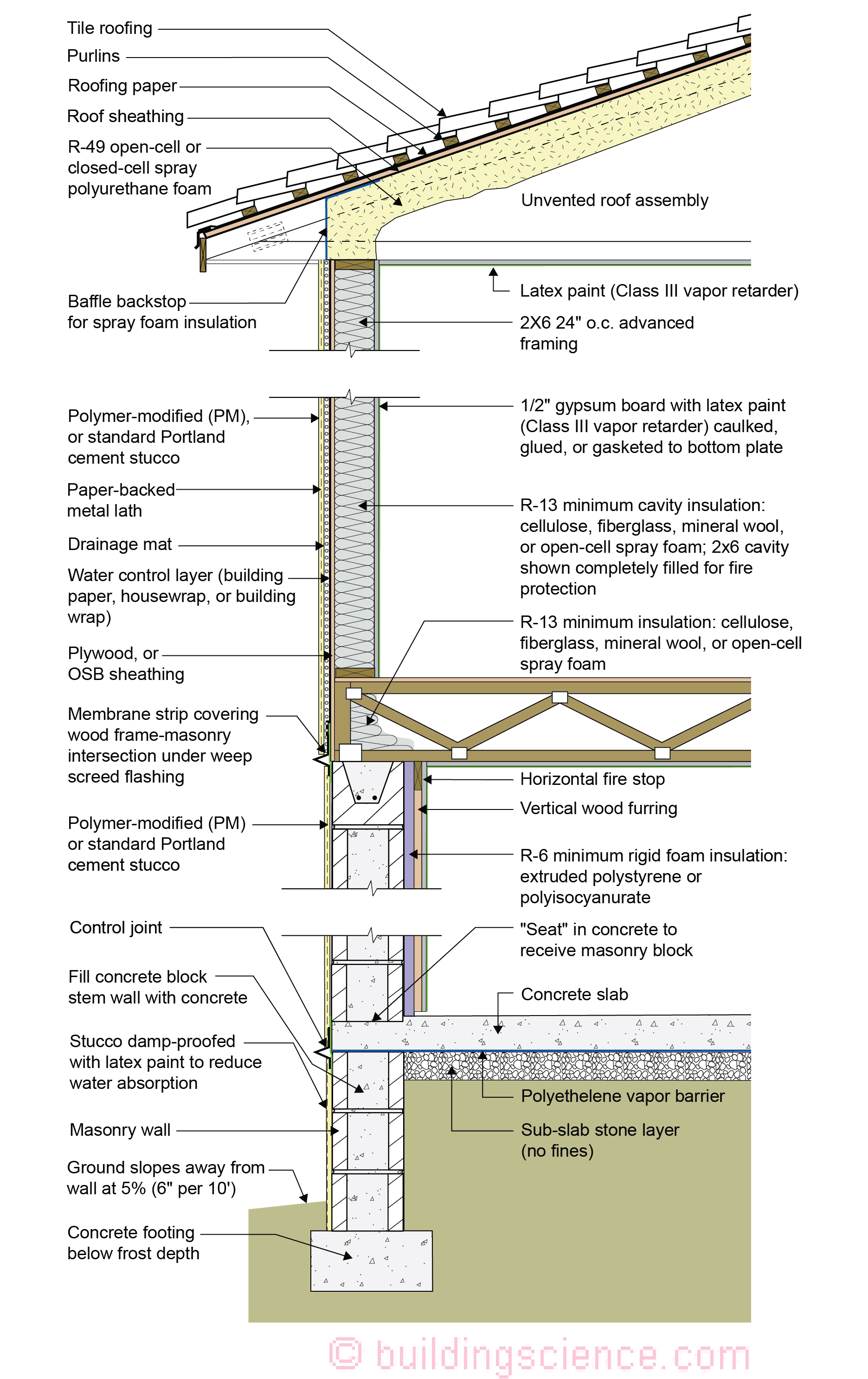
Figure 2: IECC Climate Zone 2A – Unvented attic with spray foam at roof deck, 2x6 wall, CMU wall, elevated slab.
The spray foam in the roof assembly can be either open-cell or closed-cell spray polyurethane foam. Closed-cell spray polyurethane foam significantly improves the wind uplift resistance of the roof assembly under hurricane conditions.
A drainage mat is provided behind the stucco layer installed over the frame wall to control hydrostatic pressure. This assembly is drained to the exterior at a weep screed located at the bottom of the wood framing. It should not be drained into the CMU wall.
The wood frame wall is framed with 2x6 24” o.c. advanced framing as it uses less board footage (volume of wood framing) than standard 2x4 16” o.c. framing and therefore is less expensive in material cost. It is also less expensive in labor (25% fewer framing members) and is faster to assemble. Although the code allows for 2x4 framing and lower R-value cavity insulation, the use of advanced framing and the associated cost savings more than offset the increase in the cost of cavity insulation (this of course depends on relative price fluctuations in labor and materials).
Although the minimum R-value of the insulation in this wall is R-13 per IECC, fire code may require the entire cavity to be filled, likely resulting in a higher R-value for a 2x6 wall.
Avoid vinyl wallpaper and oil-based paint or coatings in Climate Zone 2A. These wall coverings are vapor impermeable and increase the risk of condensation within the wall.
The interior of the CMU wall is insulated with rigid insulation that also controls inward vapor drive out of the CMU mass wall. The thickness of the rigid insulation is typically selected to allow electrical boxes to be installed on the interior surface of the CMU mass wall without having to chisel the masonry blocks to seat the electrical boxes. Although only R-6 rigid foam insulation is needed on the interior of the CMU wall to meet energy efficiency code, thicker insulation may be needed to accommodate electrical outlets.
The polyethylene vapor barrier under the concrete slab extends over the top of the CMU stem wall to act as a capillary break.
Portions of the CMU wall may need to be filled solid to meet structural requirements or to accommodate anchor bolts for a sill plate.
IECC Climate Zone 3B: Unvented Attic, 2x6 Wall, Monolithic Slab on Grade (Figure 3)
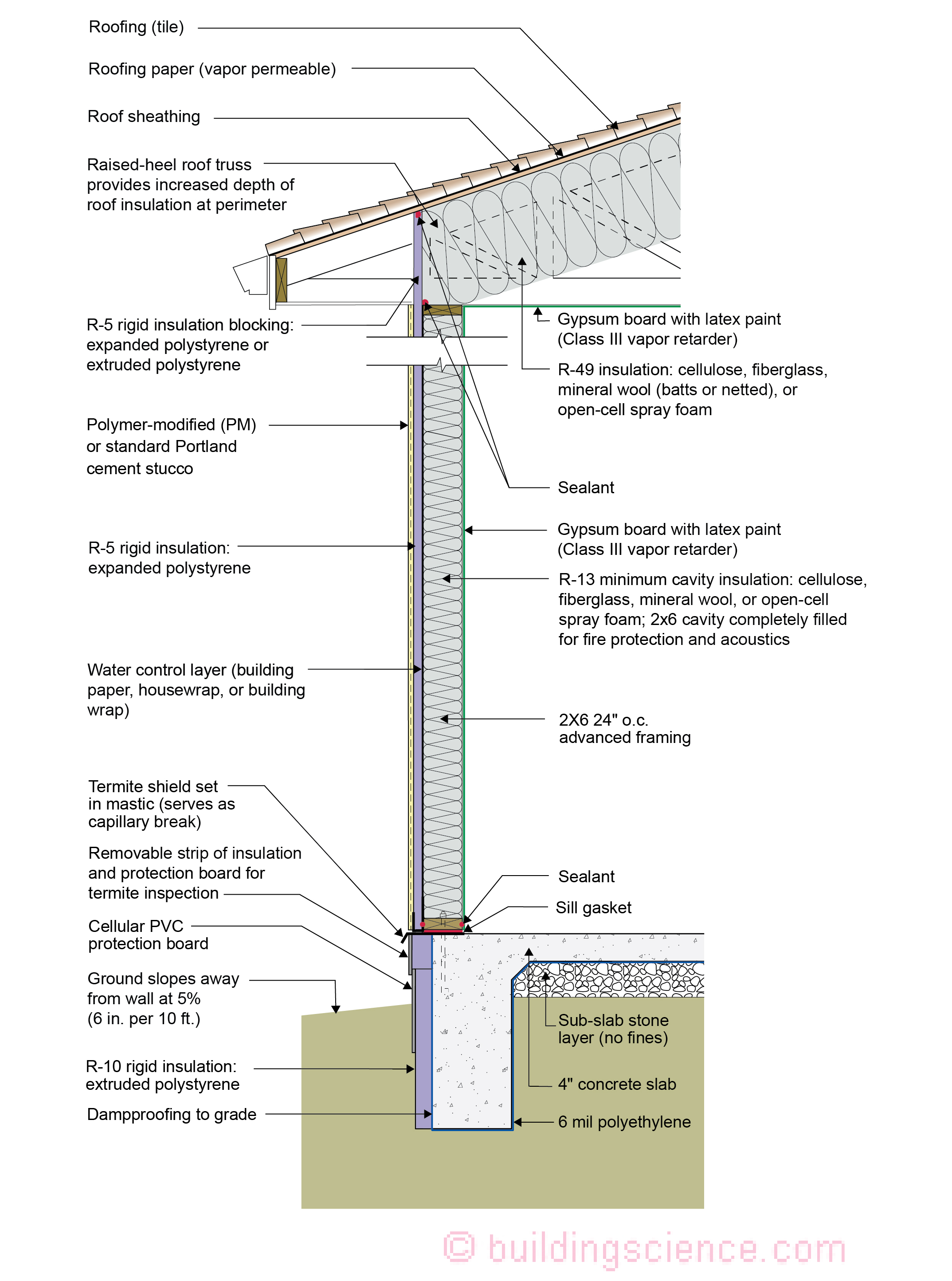
Figure 3: IECC Climate Zone 3B – Unvented attic, 2x6 wall, monolithic slab on grade.
The insulation in this unvented attic is located on the underside of the roof sheathing. With tile roofing and vapor-permeable roofing paper, no venting or vapor diffusion ports are required for this roof assembly. If the roofing material were shingles, vapor diffusion ports would be needed. Unvented attics are more resistant to entry of embers from wildfires.
The purpose of the rigid foam insulation on the exterior of the wall is to resist inward vapor drive from the absorptive stucco cladding. This wall has no structural sheathing. Instead, it has metal bracing (not shown) for racking resistance.
The water control layer in the wall assembly is installed behind the rigid insulation. Drainage occurs between the water control layer and the back side of the rigid insulation.
The wall is framed with 2x6 24” o.c. advanced framing as it uses less board footage (volume of wood framing) than standard 2x4 16” o.c. framing and therefore is less expensive in material cost. It is also less expensive in labor (25% fewer framing members) and is faster to assemble. Although the code allows for 2x4 framing and lower R-value cavity insulation, the use of advanced framing and the associated cost savings more than offset the increase in the cost of cavity insulation (this of course depends on relative price fluctuations in labor and materials).
Although the minimum R-value of the insulation in this wall is R-13 per the IECC, fire code may require the entire cavity to be filled, likely resulting in a higher R-value for a 2x6 wall.
A class III vapor retarder (latex paint) is used on the interior surface of the walls and ceiling instead of a vapor barrier. This allows drying to the interior. Avoid vinyl wallpaper and oil-based paint or coatings in Climate Zone 3. These wall coverings are vapor impermeable and increase the risk of condensation within the wall.
The rigid insulation on the exterior of the monolithic slab has a removable strip to facilitate termite inspection.
The entire monolithic concrete slab should have a polyethylene vapor barrier wrapping the underside of the slab and footing to control capillary uptake. The polyethylene should extend upward from the bottom of the footing to grade on the exterior.
IECC Climate Zone 4C: Vented Attic, 2x6 Wall, Conditioned Crawlspace (Figure 4)
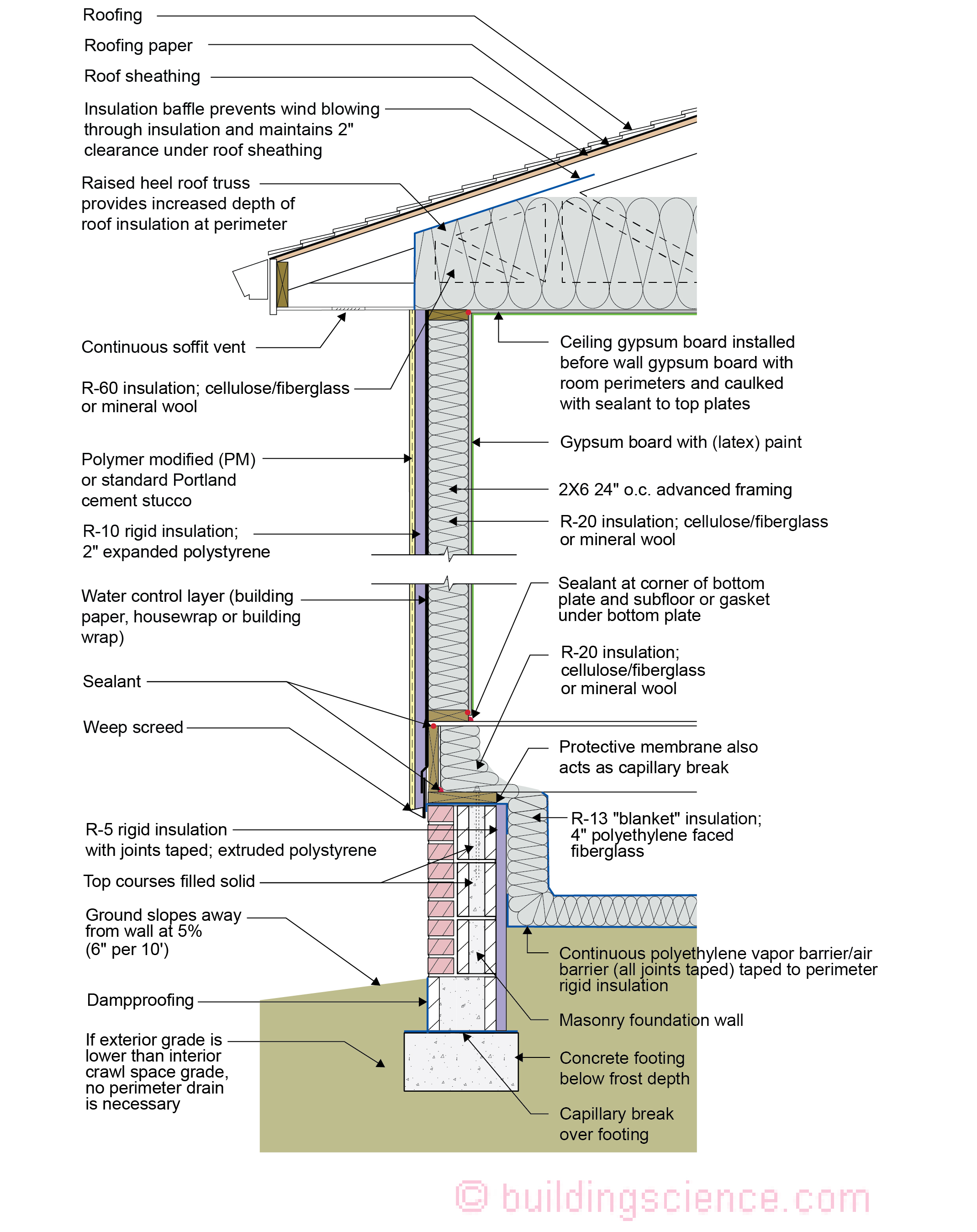
Figure 4: IECC Climate Zone 4C – Vented attic, 2x6 wall, conditioned crawl space.
The ceiling gypsum board is installed to the underside the insulated ceiling prior to the wall gypsum board in order to accommodate a “filet” bead of sealant that seals the ceiling gypsum board to the top plates creating a continuous air control layer (“air barrier”) across the entire ceiling including interior partition walls. The gypsum board is the air control layer.
The R-10 rigid insulation on the exterior of the wall framing is required to control condensation within the framing cavities as there is no interior vapor barrier – there is a vapor “retarder” (Class II vapor retarder – semi-permeable latex paint). The reason that there is no interior vapor barrier is to permit drying to the interior. The code requires approximately 30 percent of the total wall thermal resistance to be on the exterior of the frame wall to control condensation.
The function of the R-5 rigid insulation on the interior of the masonry foundation stem wall is to control condensation within the blanket insulation. The R-5 rigid insulation extends down to the footing to provide effective thermal resistance. The protective membrane strip that is installed under the sill plate and is sealed to the rigid insulation also controls entry of termites.
The masonry foundation stem wall should have the block courses filled solid with grout. The entire below grade portions of the stem wall should be coated with dampproofing to control capillary uptake.
IECC Climate Zone 5: Unvented Roof, 2x6 Wall, Vented Crawl Space (Figure 5)
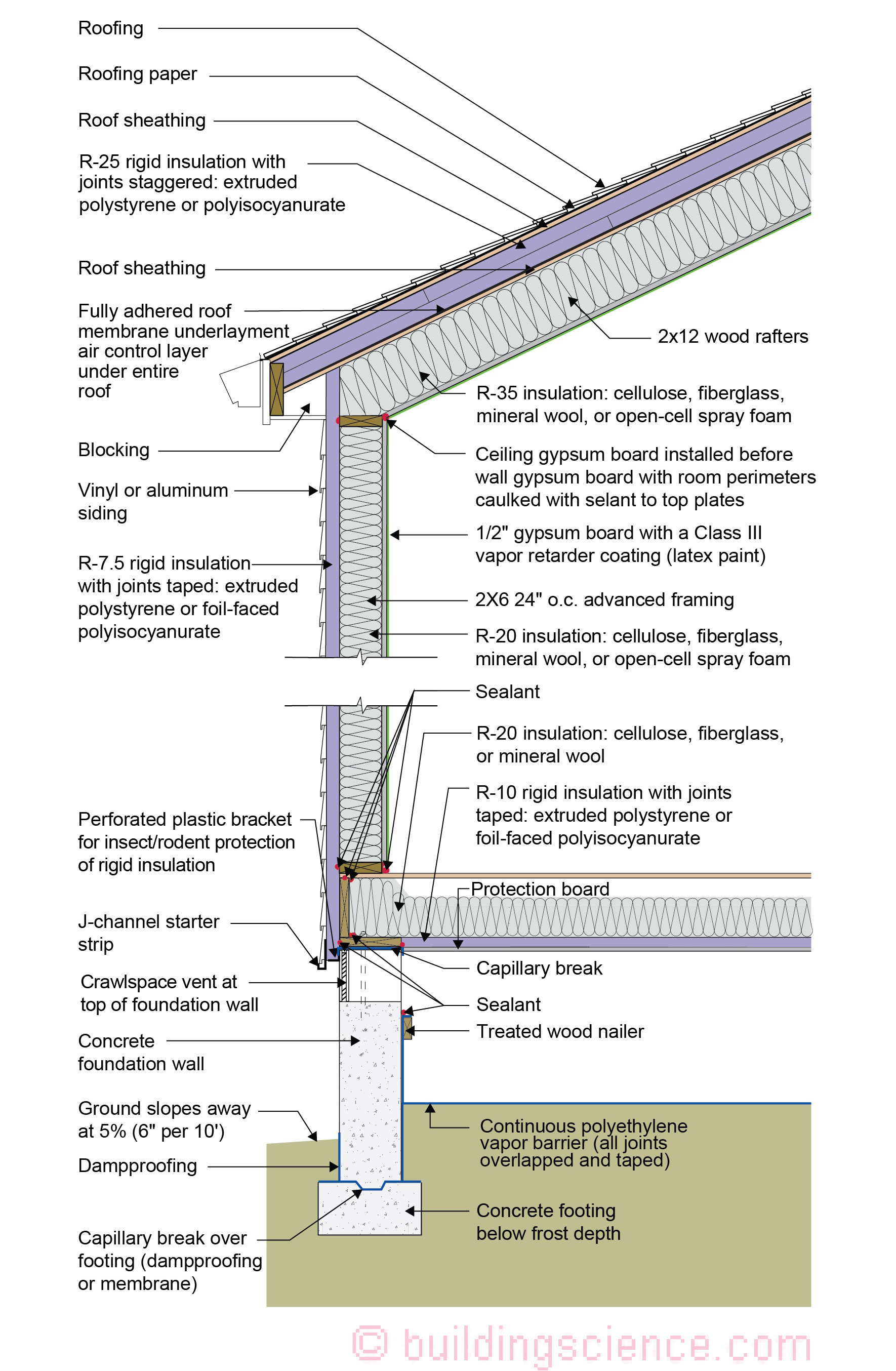
Figure 5: IECC Climate Zone 5C – Unvented roof, 2x6 wall, vented crawl space.
This unvented roof assembly should not be used where the ground snow load is greater than 50 lb/ft2 (293 kg/m2), as this assembly may not adequately prevent ice damming. Vented roofs should be used instead to control ice damming.
The rigid foam insulation at the roof deck is required to control condensation and to meet energy efficiency code (2021 IECC). There is no interior vapor barrier – there is a vapor “retarder” (Class III vapor retarder – semi-permeable latex paint). The reason that there is no interior vapor barrier is to permit drying to the interior.
The roof deck rigid foam R-value required for vapor control depends on the R-value of the cavity insulation. In Climate Zone 5, the R-value of the rigid foam should be at least R-20 per Table 806.5 of the 2021 IRC. However, if a higher amount of cavity insulation were to be used, then a higher R-value rigid foam would need to be used to control vapor. DOE-funded research has shown that the R-value of the rigid foam should be at least 40% of the total R-value in Climate Zone 5, which is more conservative than code. This drawing shows R-25 rigid insulation and R-35 cavity insulation. This meets the 40% vapor control recommendation: 25 / (35+25) = 42%). Regardless of which type of cavity insulation is used, there must not be a gap between the cavity insulation and the sheathing/rigid foam above it, per Section 806.5 of 2021 IRC. The combined R-value of the rigid foam and the cavity insulation must be at least R-60.
The wall is framed with 2x6 24” o.c. advanced framing as it uses less board footage (volume of wood framing) than standard 2x4 16” o.c. framing and has therefore been shown to be less expensive in material cost. It has also been proven to be less expensive in labor (25% fewer framing members) and is faster to assemble. This must be balanced with the difference in insulation costs for the two framing approaches.
The R-7.5 rigid insulation on the exterior of the wall framing is required per IRC Table R702.7(3) to control condensation within the framing cavities as there is no interior vapor barrier – there is a Class III vapor “retarder” (semi-permeable latex paint). The reason that there is no interior vapor barrier is to permit drying to the interior.
The rigid foam on the exterior of the wall allows construction without using structural sheathing: alternative methods of wall bracing are used instead, and the rigid foam provides a backstop for the cavity insulation as well as some structural support to the siding. Many contractors have found this to be a more economical approach.
The plastic L-bracket protecting the bottom edge of the rigid exterior wall insulation should be perforated to facilitate drainage.
The R-10 rigid insulation on the underside of the floor framing is also a vapor barrier that prevents moisture from the vented crawl space from damaging the floor framing and floor finishes. This is covered with a protection board to prevent rodents and other animals from damaging the floor assembly.
IECC Climate Zone 6: Vented Over Roof, Unvented Cathedral Ceiling, 2x6 Wall, Interior Insulated Basement (Figure 6)
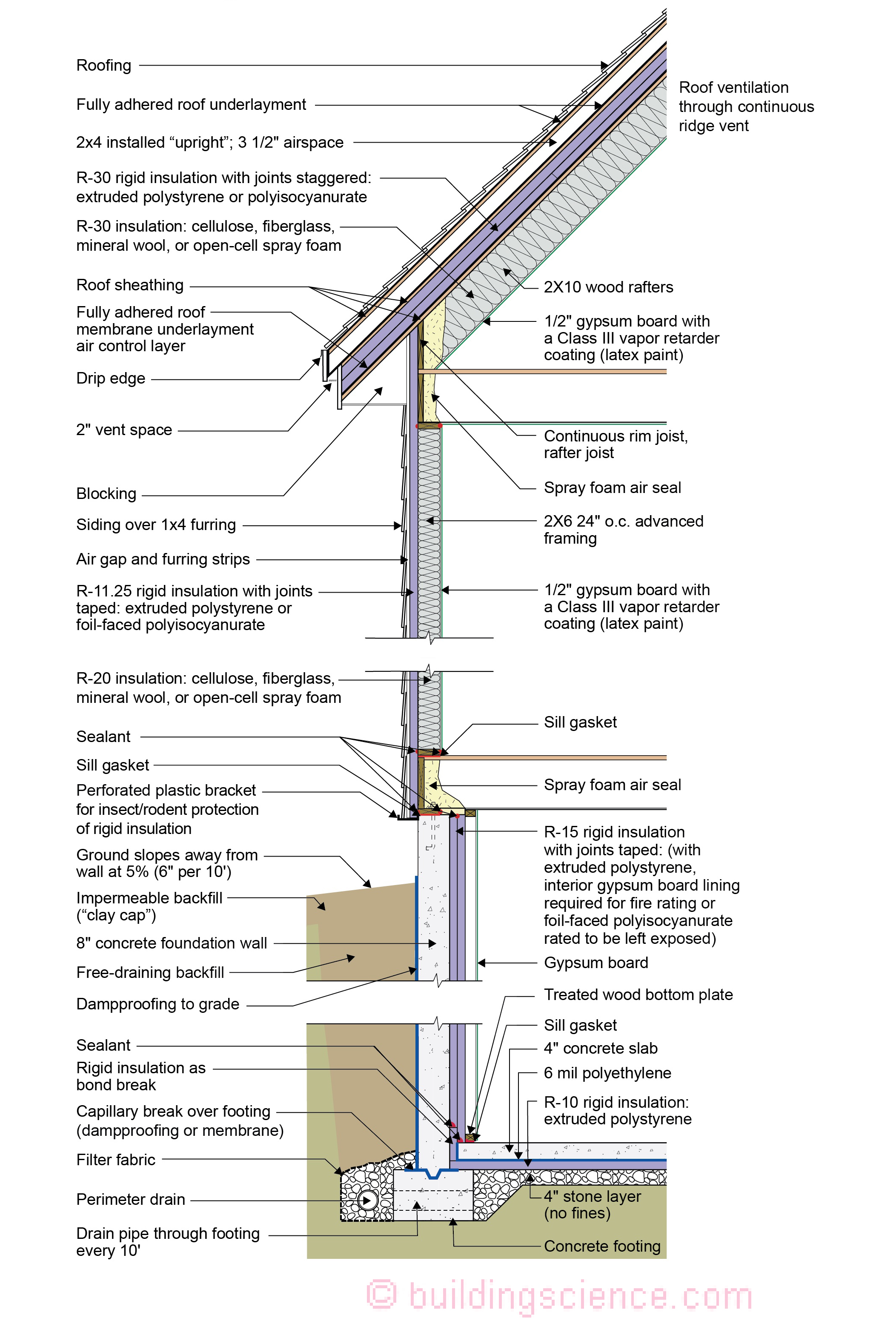
Figure 6: IECC Climate Zone 6 – Vented over roof, unvented cathedral ceiling, 2x6 wall, interior insulated basement.
The function of the “vented over-roof” is to control ice damming. Cathedral ceilings in locations with a ground snow load greater than 50 lbs/ft2 (293 kg/m2) require venting over the thermal control layer. The thermal resistance of deep snow can be high enough to allow the lower level of snow in contact with the roof to melt and cause ice damming unless the roof is vented.
There is no interior vapor barrier at the ceiling or the wall – there is a Class III vapor “retarder” (semi-permeable latex paint). The reason that there is no interior vapor barrier is to permit drying to the interior.
The rigid foam insulation at the roof deck is required to control condensation. The rigid foam R-value required depends on the R-value of the cavity insulation. In Climate Zone 6, the R-value of the rigid foam should be at least R-25 per Table 806.5 of the 2021 IRC. DOE-funded research has shown that the R-value of the rigid foam should be at least 50% of the total R-value in Climate Zone 6, which is more conservative than the code requirement. R-30 rigid insulation meets this requirement for a cavity insulation value of R-30, as is shown in the drawing (30 / (30+30) = 50%). This assembly also just meets energy code (2021 IECC). However, if a higher amount of cavity insulation were to be used, then a higher R-value rigid foam would need to be used to control vapor. Regardless of which type of cavity insulation is used, there must not be a gap between the cavity insulation and the sheathing/rigid foam above it, per Section 806.5 of 2021 IRC.
The wall is framed with 2x6 24” o.c. advanced framing as it uses less board footage (volume of wood framing) than standard 2x4 16” o.c. framing and has therefore been shown to be less expensive in material cost. It has also been proven to be less expensive in labor (25% fewer framing members) and is faster to assemble. This must be balanced with the difference in insulation costs for the two framing approaches.
With an R-20 2x6 wall, the rigid foam on the outside of the wall must be at least R-11.25 per the 2021 IRC Table 702.7(3) to control condensation within the framing cavities. There is no interior vapor barrier– there is a vapor “retarder” (Class III vapor retarder – semi-permeable latex paint). The reason that there is no interior vapor barrier is to permit drying to the interior.
An alternative to this wall assembly that meets both thermal and vapor control requirements is to use an R-13 2x4 wall with R-10 rigid foam on the outside.
The rigid foam on the exterior of the wall allows construction without using structural sheathing: alternative methods of wall bracing are used instead, and the rigid foam provides a backstop for the cavity insulation as well as some structural support to the siding. Many contractors have found this to be a more economical approach.
The plastic L-bracket at the bottom of the wall’s exterior rigid insulation should be perforated to facilitate drainage.
The vertical “short” strip of rigid insulation where the basement concrete slab intersects the exterior concrete basement wall has two lines of continuous sealant. The first seals the concrete slab edge to the interior surface of the vertical strip. The second seals the top back corner of the vertical strip to the concrete foundation wall. The two seals provide air control layer continuity between the concrete slab and the concrete wall to control radon and other soil gases.
Horizontal insulation on the underside of the concrete floor slab is provided for comfort reasons and to control dust mites in carpets by reducing the relative humidity within the carpets.
IECC Climate Zone 7 and 8: Vented Cathedral Ceiling, 2x6 Wall, Interior Insulated Basement (Figure 7)
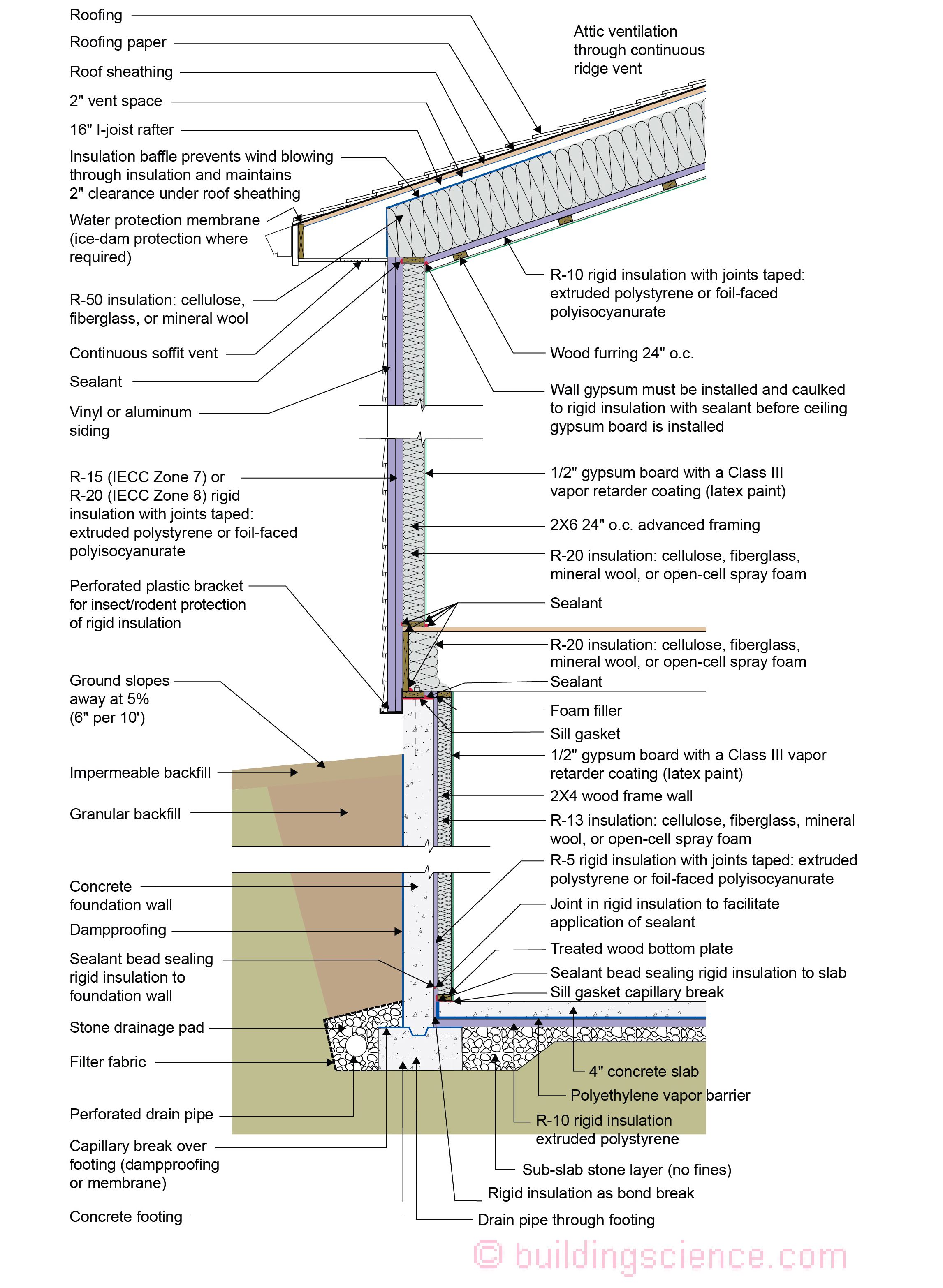
Figure 7: IECC Climate Zone 7/8 – Vented cathedral ceiling, 2x6 wall, interior insulated basement.
The R-10 rigid foam at the ceiling is not required for vapor control purposes in Climate Zone 7 as long as sufficient ridge- and soffit-venting is provided. However, it will aid the control of moisture by slowing vapor transfer from the conditioned space to the roof assembly. The rigid foam brings the total roof R-value up to the 2021 IECC requirement of R-60. Because the I-joist rafter is 16 inches and a 2-inch ventilation space is needed above the insulation, only about 14 inches are available for the fibrous cavity insulation. This will typically give an R-value of about R-50, leaving the need for the R-10 rigid foam. Note that only 1 inch of ventilation space above the cavity insulation is required by code, but 2 inches is recommended in areas where ice damming could be an issue or where rafter spans are long. The rigid foam at the ceiling is also used to allow the creation of a service raceway between the rigid foam and the gypsum board below it. The rigid foam acts as the air control layer instead of the gypsum board. The service raceway allows the air control layer to be undisturbed by the electrical penetrations in the ceiling. A third purpose of the rigid foam in this application is that it also reduces drywall cracking. From a vapor control standpoint, however, the rigid foam and the raceway are not required by 2021 IRC, and R-60 fibrous cavity insulation could be installed directly on top of the gypsum board if cavity height allows and if the attic is properly ventilated. In this case the gypsum board would become the air control layer and would need to be carefully sealed, and a Class I or II vapor retarder paint would be recommended at the ceiling.
The wall is framed with 2x6 24” o.c. advanced framing as it uses less board footage (volume of wood framing) than standard 2x4 16” o.c. framing and has therefore been shown to be less expensive in material cost. It has also been proven to be less expensive in labor (25% fewer framing members) and is faster to assemble. This must be balanced with the difference in insulation costs for the two framing approaches.
The R-15 or R-20 rigid insulation on the exterior of the wall framing is required by 2021 IRC Table 702.7(3) to control condensation within the framing cavities. There is no interior vapor barrier on the interior surface of the wall – there is a vapor “retarder” (Class III vapor retarder – semi-permeable latex paint). The reason that there is no interior vapor barrier is to permit drying to the interior.
For Climate Zone 8, this assembly does not require any cavity insulation per 2021 IECC due to the R-20 continuous rigid foam. However, filling the cavity may be needed or preferred for fire protection, acoustics, and energy efficiency.
An alternative to this wall assembly that meets both thermal and vapor control code requirements is to use an R-13 2x4 wall with R-10 (climate zone 7) or R-12.5 (climate zone 8) rigid foam on the outside.
The rigid foam on the exterior of the wall allows construction without using structural sheathing: alternative methods of wall bracing are used instead, and the rigid foam provides a backstop for the cavity insulation as well as some structural support to the siding. Many contractors have found this to be a more economical approach.
The R-5 rigid insulation on the interior of the concrete foundation wall is required to control condensation within the interior frame wall as there is no interior vapor barrier on the interior of the frame wall – there is a Class III vapor “retarder” (semi-permeable latex paint). The reason that there is no interior vapor barrier on the interior of the frame wall is to permit drying to the interior. Additionally, the R-5 rigid insulation on the interior of the concrete foundation wall reduces the rate at which moisture contained in newly placed concrete moves to the interior.
The plastic L-bracket protecting the bottom edge of the exterior rigid insulation should be perforated to facilitate drainage.
The vertical “short” strip of rigid insulation where the basement concrete slab intersects the exterior concrete basement wall has two lines of continuous sealant. The first seals the concrete slab edge to the interior surface of the vertical strip. The second seals the top back corner of the vertical strip to the concrete foundation wall. The two seals provide air control layer continuity between the concrete slab and the concrete wall to control radon and other soil gases.
Horizontal insulation on the underside of the concrete floor slab is provided for comfort reasons and to control dust mites in carpets by reducing the relative humidity within the carpets.